Metropolitan Atlanta Rapid Transit Authority
Customer Spotlight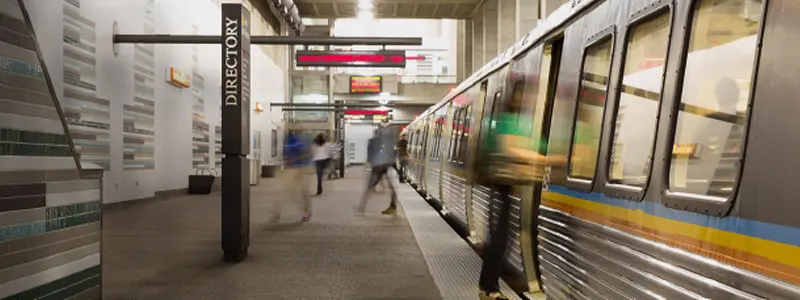
Major transit agency cleans up, fixes what’s broken, and saves time.
The Metropolitan Atlanta Rapid Transit Authority (MARTA) is the eighth largest in the U.S. In addition to its rail service, the agency’s 530 buses serve more than 100 routes across 1,400 miles, and transport nearly 100,000 riders each weekday. Providing safe, reliable transit service and clean stations is a responsibility MARTA takes seriously.
As does Timothy Parson, a engineer and Lean Practitioner in MARTA’s Department of Safety and Quality Assurance. Parson is responsible for improving processes throughout the agency.
After joining MARTA, one of Parson’s first assignments was to execute the Zonar V4 telematics control units (TCUs), which were pre-installed by the fleet’s OEM bus providers.
Modern tech solves fleetwide problems.
Having OEM-grade TCUs enabled Parson to open visibility across the fleet, without adding installation costs.
With essential, real-time fleet data, including bus locations, historical paths and routes, he addressed some of MARTA’s toughest challenges.
- Ill-fitting routes for longer buses caused incidents.
- Community citizens were lodging speeding complaints.
- Avoidable repair costs needed to be controlled.
MARTA implemented Zonar EVIR, an added Zonar solution, to digitize MARTA’s paper-based vehicle inspection system and ensure safer, more reliable buses. EVIR will also help MARTA ensure cleaner safer stations, facilities and tunnels.
Buses turn corners without collisions.
MARTA’s longer buses were contacting with telephone poles and stop signs while turning because their routes were too narrow for their dimensions. A fact that MARTA discovered by looking at the buses’ inspection reports and trip data on the secure, online Zonar Ground Traffic Control portal.
Buses showed visible damage, so MARTA viewed their routes, start to finish. And MARTA discovered that the longer buses couldn’t fit through narrow openings or cleanly complete tighter turns, resulting in sideswipes. Routes were analyzed so right-size buses could be used to maneuver. Maintenance and repair costs went down because vehicles sustained less damage.
Data proved operators’ safe driving.
Any fleet that serves the public needs data to investigate calls of concerns. Citizen reports stated that MARTA transit buses were speeding through neighborhoods and shaking houses.
To investigate, the Zonar Customer Success team helped MARTA set up geofences within Ground Traffic Control around these areas.
When the fleet’s actual speeds were compared against the reported issues, Zonar V4 data showed that operators were obeying the speed limits.
- Operators were exonerated of excessive speeding.
- The agency maintained a positive relationship with its communities.
- Citizens discovered that another source caused the problems.
Paper forms left buses unrepaired.
Bus operators were using a a paper-based system to perform required bus inspection. This system opened the door for natural human errors.
- Defects could go unnoticed or unreported.
- Repairs may be delayed or unmade.
- Maintenance requests could get lost.
Due to their system, buses could be sent out without necessary repairs. To address these gaps in process, MARTA introduced Zonar EVIR.
Now those buses stay home sick.
MARTA operators now use EVIR to electronically verify proper, thorough inspections; no paper forms.
Drivers physically visit each zone and scan the Zonar tag with a Zonar 2010 handheld device. They follow the inspection procedure displayed on the screen, and upload the results to the Zonar Ground Traffic Control.
Results are immediately available for online review. Each part of the inspection is also date and time stamped so managers can tell if any zone or inspection was rushed or skipped.
- Pencil-whipping has been eliminated.
- Repair requests are digitally sent to maintenance.
- Defects are prioritized instead of lost in a box.
- Buses that need repair are kept out of service.
- Digital inspection records are retained instead of paper.
MARTA’s maintenance team collates all defects identified during EVIR inspections. When the bus returns to the yard, mechanics have been alerted to the necessary repairs.
Buses spend less time in the shop because defects are addressed sooner. And potentially unsafe buses are less likely to suddenly be pulled from service because they’re pulled until repaired.
No more need for more storage.
When operators performed paper-based inspections, physical records were stored in a brick-and-mortar facility to meet retention requirements. Over time, the forms accumulated, filling the space.
Using EVIR to digitize inspections and their records eliminated the need for added storage space.
Operators use EVIR’s check-in attendance feature at the start of their bus inspections. This check-in feature ensures that all operators check in before their shift, and that everyone is accounted for.
On and off the bus, EVIR keeps people safe.
As one of the nation’s largest transit agencies, maintaining MARTA’s standard of cleanliness and safety has grown more difficult.
People who use public transit naturally leave their foot-print. Travelers who ride the buses and trains also use the stations’ facilities, so it’s essential to keep buses and stations clean and safe for patrons.
Inspections and sanitations are verified.
Parson, with the help of his team, strategically put EVIR to work ensuring inspections and sanitations throughout stations.
Parson explains. “I was deliberate where I placed the discs, so that it drives sanitation workers to check certain areas so that the cleaning is thorough.”
Each inspection is date and time stamped, giving MARTA “the liberty of seeing exactly when they clean the station, how long it took them to clean, and what might have been reported.”
And people are protected from harm.
EVIR tags were placed in areas where people sleep, so transit workers know to check these danger zones for inhabitants.
These areas are also inspected for brush and overgrown trees to reduce the likelihood of fires. Parson says, “EVIR helps us monitor areas that need to be cleared for fire safety.”
Coming up: More work for EVIR.
The task of assessing, implementing and managing Zonar fleet technology has been Parson’s primary task since he came on board with MARTA.
With the help of Zonar Customer Success, MARTA has transformed how inspections are performed and how operations are managed using Zonar smart fleet management and mobility solutions.
MARTA plans to expand its use of EVIR to maintain sanitation standards at bus stations and waysides by integrating the inspection reporting into their work order system.
Work orders would be generated immediately rather than waiting for the inspection to conclude. Issues will be prioritized and addressed sooner, and station sanitation will grow more proactive.