Sidestep these pitfalls of self-installing fleet telematics.
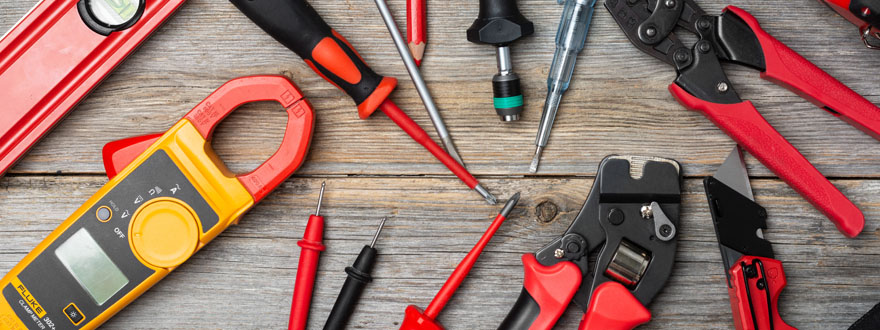
Avoid rolling out the welcome mat for problems.
Capturing high-quality data from complex commercial fleet vehicles and assets requires an OEM-grade telematics solution. Big commitment, big project, big impact on operations. Relying on your own staff, technicians and maintenance teams to coordinate and install the telematics control units (TCUs) is a tempting option to save money and resources.
“What could go wrong?” More problems, downtime and lost costs than you were trying to avoid.
- Malfunctioning or incompatible devices can’t deliver reliable data, so the system doesn’t work.
- Lack of hardware installation expertise results in costly, unnecessary vehicle or asset damage.
- Improper electrical connections and faulty wiring can create fire hazards.
- Unspecialized project management overlooks inventory and vehicles, and extends deadlines.
- In-house staff and technicians are stretched beyond their capacity to support daily operations.
- Lack of thorough quality control throughout the process fails to prevent downstream issues.
Some fleets are equipped and able to self-install complex, commercial telematics systems. Others are not. Before you commit to self-install, let’s cover some common pitfalls.
Assuming complex TCUs are simple enough to install yourself.
Complex TCUs for commercial vehicles pull high-quality data directly from the engine control module (ECM). Not all telematics devices are compatible with all fleet vehicles and assets. Connections and placements will differ based on the make, model and year of the fleet vehicle or asset, as well as other aftermarket equipment connected to the vehicle.
Trying to install the TCUs without expert knowledge of the hardware, equipment, vehicle connections and best practices raises the risk of incompatibilities and complications. Your teams may be experts in maintaining your fleet, but they may not be the experts in telematics technology that a professional install team will.
In-house technicians and maintenance | Professional fleet telematics installers |
---|---|
Twice the hours (plus) to install each TCU Knows your fleet’s vehicles and assets Less familiar with the telematics technology Likely specialized in vehicle mechanics, not electronics More likely to unnecessarily damage vehicle or asset Balances installation with daily responsibilities Ill-prepared to troubleshoot or prevent issues Lacks expertise to properly QC the telematics system |
Minimal time to install each TCU Knows most types of fleet vehicles and assets Specializes in the telematics technology Unlikely to unnecessarily damage vehicle or asset Is insured to cover repairs, if necessary Focuses exclusively on performing a proper install Expert in detecting, addressing and preventing issues, and escalating when necessary Performs a thorough QC to ensure working system |
Self-installation without in-depth knowledge of the telematics system raises the risk of accidentally causing unnecessary damage. Some yellow iron construction fleet assets have a purchase price into the millions of dollars; repairs don’t come cheap. Plus, many fleet vehicles and assets are essential for keeping operations in motion. When critical vehicles aren’t rolling or job-stopping assets aren’t working, neither is anyone else.
Predicting that self-install will be faster than it really is.
Time spent installing OEM-grade TCUs is time taken from supporting everyday operations. With or without in-house expertise, self-install takes longer than professional fleet telematics installation.
- The learning curve to the hardware, its installation, and connecting it to the software limits your team’s ability to make the deadline.
- Additional, unplanned time for troubleshooting upfront and downstream issues pushes the deadline and requires more resources.
- Fitting telematics installation time into staff schedules around daily responsibilities means that one will take priority over the other.
Even technicians who are qualified to install complex fleet telematics have other daily priorities that come first. Given the shortage of mechanics and techs, your in-house team’s need to work around packed daily schedules extends the telematics installation timeline.
Not realizing the cost of lost and excess inventory.
Telematics hardware is hard budget costs. Yet, due to inexperience, fleets often mismanage the inventory. And they fail to realize the importance of tracking where which TCUs are sent and confirming that correct inventory arrives safely, especially across locations.
Each device, plus its installation hardware and connectors, need to arrive at the correct destination in time for the scheduled install. Not tracking telematics hardware in detail invites a host of problems, all of which will consume the time, money and other in-house resources that you were trying to save.
- Downstream inventory issues create additional vehicle downtime.
- Ordering replacements costs more money and takes more time to ship.
- Staff, technicians and personnel spend additional time tracking down wayward inventory.
- Overlooked TCUs and their hardware take up physical storage space until cleared.
Overlooking the value of dedicated telematics project management.
A fleetwide, commercial telematics installation entails coordinating logistics, vehicle availability, telematics inventory, install schedule, and installer accessibility across locations. The person tasked with the project’s management may not know how to keep this multitude of moving parts from going off track. Nor have time to oversee every detail.
- Hardware is sent in wrong quantities to wrong locations.
- Physical install schedules are misaligned with vehicle availability and fleet operations.
- Fleet vehicles and assets miss their installation window and need to be rescheduled.
- Downstream issues and delays accumulate due to early mistakes and oversights.
- Daily operations suffer when in-house personnel juggle daily responsibilities and project management.
- High pressure to deploy and utilize the telematics system as soon as possible impacts the project team’s ability to focus and perform effectively.
Consider professional fleet telematics installers for their dedicated expertise.
Even technicians who can perform the complex telematics installation themselves should consider engaging the provider’s professional installation services. Free your teams and personnel to focus on what they do best: supporting day-to-day operations. And consider inviting a professional telematics installation team to do what it does best: install your fleet telematics technology.
- Specialized expertise and dedicated focus for planning, installing and verifying the workmanship
- Trained to quickly troubleshoot inevitable issues and prevent downstream issues
- Fully dedicated to installing your TCUs safely and efficiently, without missing a detail
- TCU hardware and equipment inventory management, even across locations
- Tracking installs, including unavailable vehicles and assets such as those deployed, lost or in the shop for repairs
To learn what to expect in professional fleet telematics installation, download our whitepaper.
FAQ
Q: Does every telematics installation require enterprise-class installation services?
No. Plug-and-play, light-duty TCUs are appropriate for capturing data on OBD-II equipped vehicles such as passenger trucks and vans. The professional installation discussed in this article is recommended for OEM-grade TCUs on more complex fleet assets such as commercial big rigs, construction yellow iron, specialized utilities vehicles, and pupil and transit buses.
Q: What if I’ve already started my fleet’s self-install?
Work with a professional installation team to reassess and course correct.
Can’t my team just follow the instructions my telematics vendor gave us?
They could. But do your in-house technicians have the time and expertise to guarantee a proper fleet telematics installation? Moreover, do you want them installing hardware on fleet vehicles and assets that cost thousands, tens of thousands or even millions of dollars?
Even if they’re fully qualified to do so, the learning curve is steeper and the installation process takes more time than a professional installation team would require.
Q: What else could a professional installation team offer that my in-house team can’t?
Specialized, role-based training and onboarding to get you up and running more effectively, faster. Start using the solution sooner and focus on optimizing your operation instead of learning and troubleshooting your new fleet telematics.
Q: What should I look for in a professional installation team?
Experts who know their technology and how to get in, perform an efficient and thorough installation, and minimize their impact to your daily operations. To learn more, download our whitepaper.